Goals
Our laboratory works on the following research themes to realize a sustainable society.
- Support and automation technologies for an aging society
- Research on robot intelligence
- Research on robots that support humans with soft mechanisms and control
- Research on high-level automation of construction machinery
- Research on environmental recognition and motion planning using machine learning
- Technologies that contribute to solving the problem of climate crisis
- Energy-efficient electrical-mechanical energy conversion
- Electrical-mechanical energy conversion based on new principles
- Electrical, mechanical, and thermal energy conversion for climate control
We conduct research primarily in control applications for robots and electromechanical systems, as well as system optimization for production systems and related areas. In particular, in response to pressing societal challenges such as the aging population and climate crisis, we are engaged in the development of robots aimed at supporting the independence of disabled people and reducing the burden on medical and caregiving professionals. Our work also includes research on automatic tuning of control parameters to improve quality and optimal motion planning for various autonomous construction machinery to enhance productivity.
Additionally, we are investigating actuators that improve the energy efficiency of electric vehicles and robots, as well as engineering methods to mitigate typhoon impacts and harness energy from typhoons. We actively promote the social implementation of our research seeds and are conducting numerous collaborative studies with both domestic and international companies.
Research Topics
Data-Driven Simulation
Patent JP7256327B1
Bilateral Drive Gear
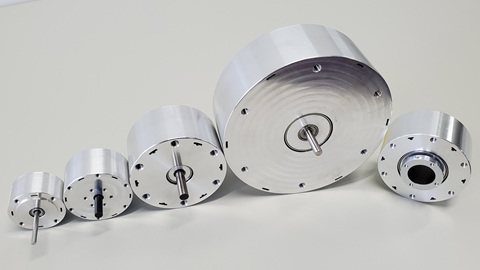
Pantent JP6782494B2,
US11181170B2
CN109312823B
Autonomous Mobile Robot
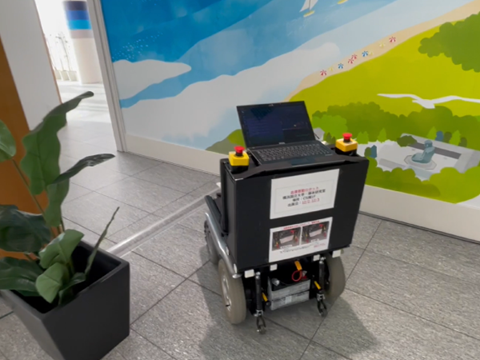
Rehabilitation Robots
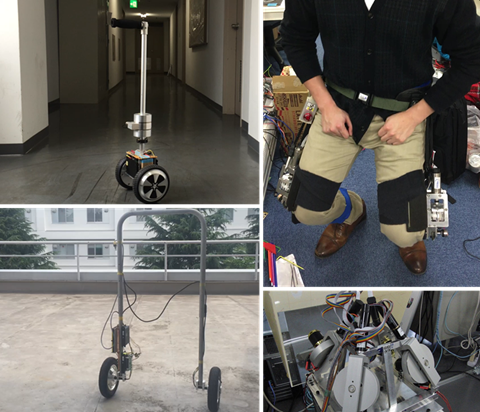
Patent JP7108298B2
Compact Air-cooled Motor
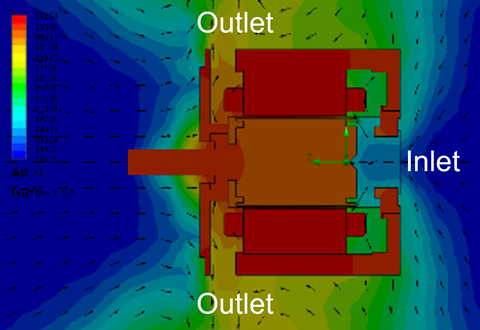
Patent JP7164881B2
Resonant Motor
Patent JP6537930B2
Helical Motor
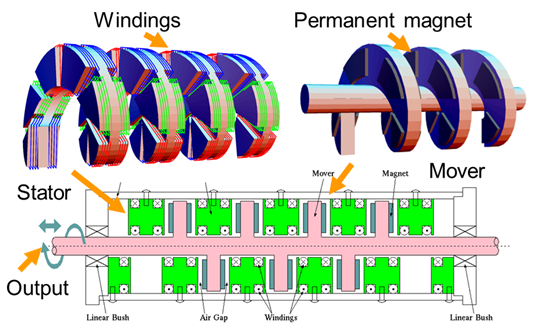
Patent JP3712073B2,
US7176590B2,
CN100466426C,
EP1560320A4,
AU2003275656A1,
KR100720266B1
Nine-Switch Inverter
JP2009050042A
Contact
Yasutaka Fujimoto
Graduate school:
Specialization in Electrical and Computer Engineering,
Graduate School of Engineering Science
Undergraduate school:
Educational Program for Electrical and Computer Engineering,
School of Engineering Science
Concurrent position:
Research Center for Next-Generation Health Technology /
Typhoon Science and Technology Research Center,
Institute for Multidisciplinary Sciences
email: fujimoto (please add the university's domain name.)
Access
79-5 Tokiwadai, Hodogaya-ku, Yokohama 240-8501 JAPAN
Room 401/403, Engineering Science Lab., Yokohama National University
Bld. S5-6 in Campus map